We recently hosted a live stream where our CEO and Head of
Technology, Duncan, looked into and explained the essential transition from candle development to full-scale production. Whether you’re a budding entrepreneur or an established small business, this guide captures the key points from our session, ensuring you’re equipped with the knowledge to streamline your operations and boost your efficiency.
Candle development to production livestream
Understanding the Business Essentials
Every business, regardless of its nature, revolves around
three core activities:
Marketing and Sales: Identifying and engaging with your target market to create demand and drive sales.
Product Development: Creating products or services that meet your market's needs and offer value.
Production and Operations: Ensuring consistent delivery of your products or services.
The focus of our live session was on the third aspect – theintricate world of production and operations.
Common Production Challenges
As you scale up from a small operation to a more structured business, it’s common to encounter several production hurdles:
• Incorrect raw material usage (e.g., wrong wax or fragrance).
• Inventory mishaps, such as missing or overstocked items.
• Inefficient production planning leading to delays and extra costs.
If any of these issues resonate with you, know that you're not alone. Running a manufacturing business is inherently complex, but with the right systems in place, you can navigate these challenges effectively.
Breaking Down the Production Process
During this video we looked through a detailed production journey, highlighting the importance of meticulous planning and control:
1. Recipe Management: Documenting your product formulations (also known as Bills of Materials or BOMs) ensures consistency.
2. Work Orders: These guide your production runs, specifying the quantities and materials needed.
3. Raw Material Inventory: Keeping track of stock levels to avoid shortages and overstock.
4. Purchase Planning: Ensuring you order just the right amount of materials at the right time.
5. Production Scheduling: Planning your production runs based on sales forecasts and inventory levels.
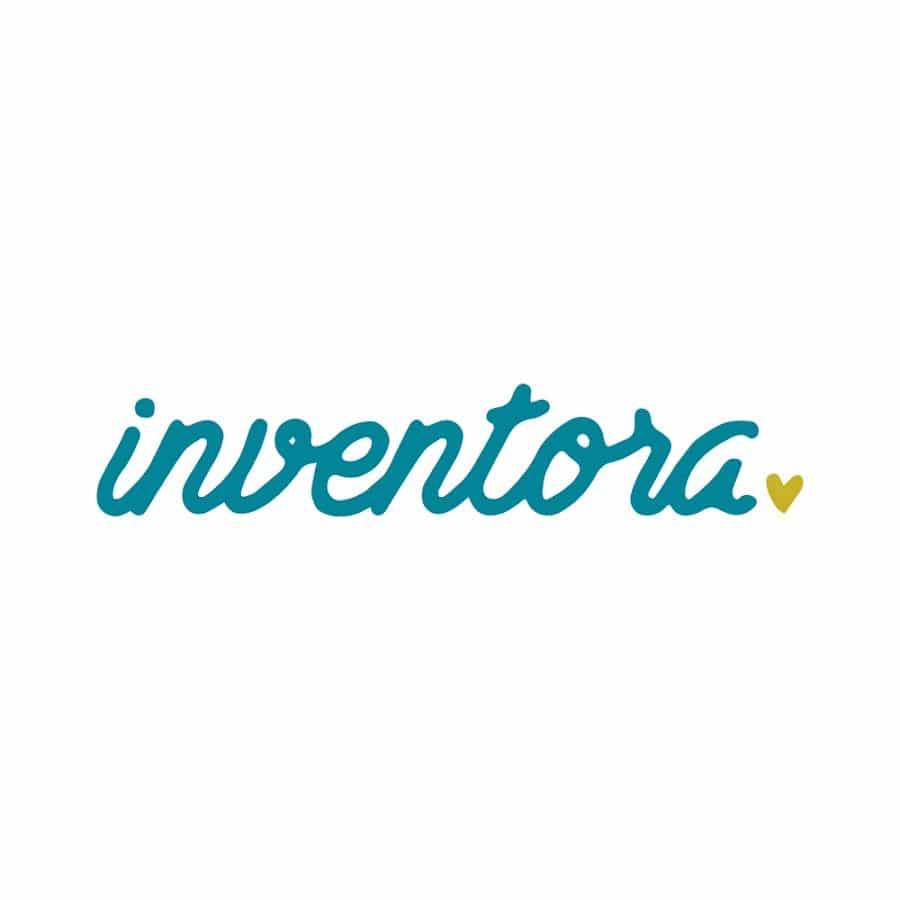
The Power of Systems
Large companies use sophisticated ERP (Enterprise Resource Planning) and MRP (Manufacturing Resource Planning) systems to manage these processes. However, these solutions are often prohibitively expensive and complex for small businesses.
For smaller operations, systems like Inventora, an intuitive and affordable mini-ERP designed for makers and small manufacturers are recommended. Inventora offers functionalities such as:
Inventory Management: Tracking raw materials and finished goods.
Production Planning: Scheduling and managing production runs.
Batch Tracking: Ensuring traceability of materials and products to manage quality and recalls.
Why Inventora?
Inventora stands out because it’s crafted by makers, for
makers. The interface is user-friendly, and it integrates seamlessly with your
existing workflow. Additionally, we've partnered with Inventora to offer a 20%
discount for our community.
Streamlining your production process is crucial for maintaining quality and profitability. With tools like Inventora, you can transform your small business operations and focus more on growth and innovation.