In a recent live session, we shared invaluable insights on maintaining and improving quality in candle production. As businesses scale up, especially during busy seasons, these best practices become crucial. Here's a detailed summary of the session, highlighting key points and strategies.
Quality assurance in a growing candle business
Stage 1: Viability and Testing
Development Sheet:
- Business owners should meticulously record their experiments with various fragrances, waxes, glasses, and wicks.
- Costing is vital, particularly for expensive materials like essential oils, to ensure the products are economically viable.
- Safety tests are essential to verify that the candles burn correctly, emit pleasant aromas, and are easy to produce.
Bill of Materials (BOM):
- A master document for each product, listing all ingredients and quantities, should be created.
- Including a revision number and date helps track any changes over time.
- Establishing a build multiplier, such as producing candles in multiples of the number of jars in a box, can streamline production.
Costing Sheet:
- Tracking the actual costs of materials and labor refines pricing strategies.
- Development documentation and test reports serve as evidence of a product's safety and quality.
Stage 2: Production and Quality Control
Work Orders:
- Work orders, derived from the BOM, act as job cards for each production run.
- Each work order should include a unique reference number, batch number, component list, and planned vs. actual quantities produced.
- For large quantities, separate work orders for each day's production can better track potential errors.
Pick Sheet:
- Based on the BOM, pick sheets ensure the correct quantities of materials are available for each production run.
Packing Specification Document:
- A detailed, illustrated guide for packing products helps maintain consistency and quality.
- Quality control checks for weight, defects, and proper packaging should be included.
Retain Samples:
- Keeping samples of larger production runs helps monitor for potential issues, such as discolouration or fragrance changes, over time.
- Proper storage of samples allows for comparison with customer complaints and verification of storage conditions.
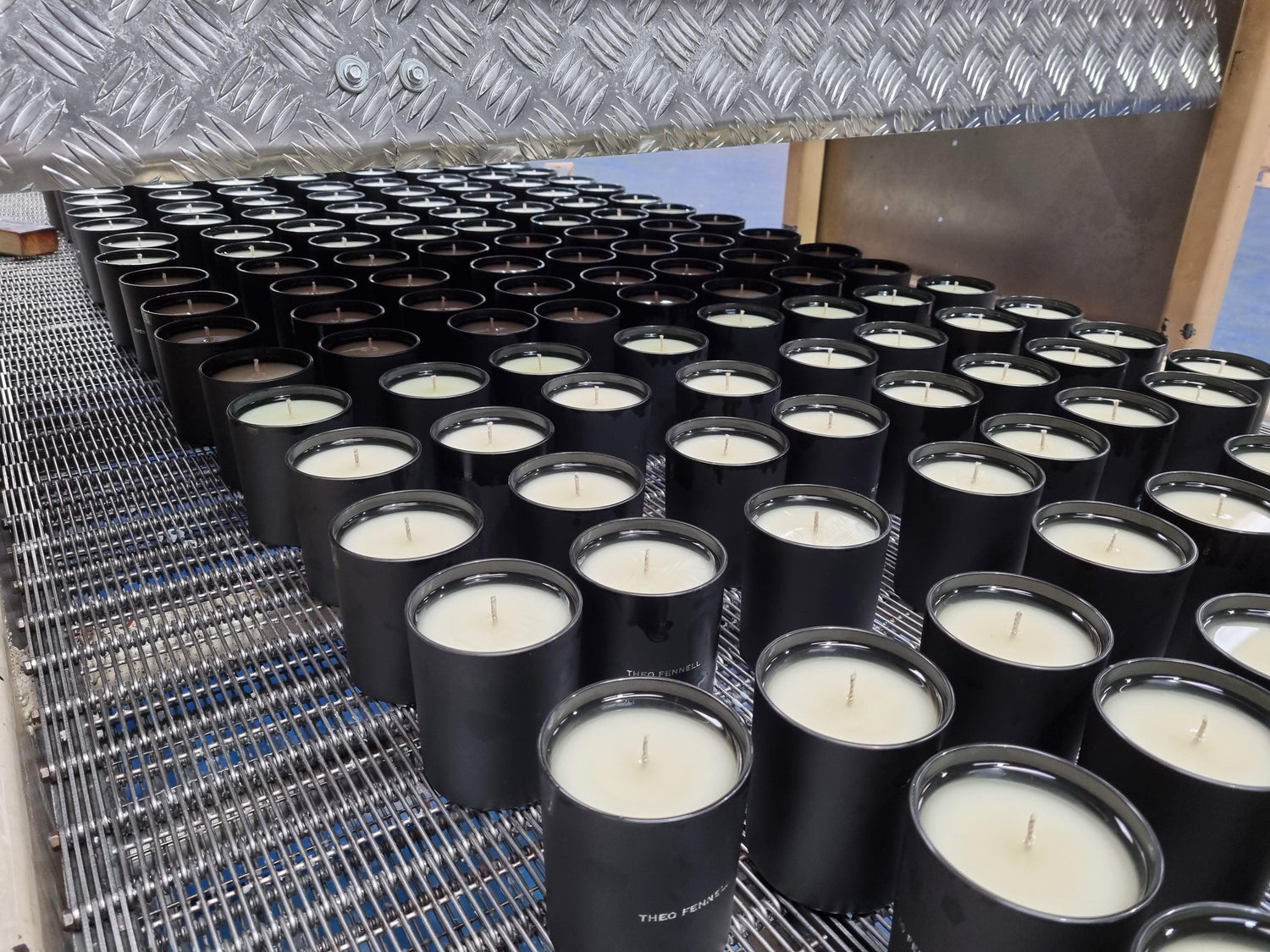
Stage 3: Review
Review and Adjust:
- Comparing actual production costs and materials used with initial estimates highlights areas for improvement.
- Adjusting the BOM and work orders based on discrepancies improves accuracy and efficiency.
- Tracking labor hours and material usage refines cost calculations and pricing strategies.
Practical Tips
Standardize Production: Consistent production quantities minimise errors and simplify batch tracking.
Document Everything: Detailed records of all aspects of production, including development, production runs, and quality checks, are essential.
Use Templates: Templates for BOM, work orders, and packing specifications streamline processes.
Burn Your Candles: Regularly burning candles allows for performance monitoring and early detection of issues.
Tools and Resources
Inventora Integration:
- Inventory management software like Inventora can automate tracking, purchasing, and stock level adjustments.
- Features include materials and products tracking, automatic cost calculations, and e-commerce integration.
Costing Tools:
- Online calculators help determine the required quantities of wax and fragrance for production runs.
Effective quality management is crucial for growing candle businesses. By implementing best practices and leveraging tools like Inventora, business owners can ensure their products remain high-quality and cost-effective.
For any questions or further assistance, business owners are encouraged to reach out. The Candle Shack team is dedicated to supporting their success in the candle-making journey!